
- BELL CRANK DESIGN EXAMPLE CRACK ROD IS
- BELL CRANK DESIGN EXAMPLE CRACK IN THE
- BELL CRANK DESIGN EXAMPLE CRACKED ROD IS

Automobile designers for passenger vehicles use the softer suspension setups as the goal is to provide comfort and stability while the Race car Designers choose the firmer settings to achieve improved handling and performance at high speeds considering the cornering loads and down-forces.Conventionally for Sports cars the springs were placed on the unequal length Suspension Arms (Double Wishbone Arms) # which used to get in the way of the air flow and thus reduces the aerodynamic abilities of the car. So in push/pull systems the damper can be placed inside the chassis easily which thereby improves the aerodynamics. Another advantage of using such setting is the adjustabilty which can be achieved by incorporating a adjustable type bell- crank (rocker arm) design in the system. Notice that if rocker in Figure is very long, it can be 4 replaced by a block sliding in a curved slot or guide as shown.
Bell Crank Design Example Cracked Rod Is
Bell Crank Design Example Crack Rod Is
The dynamical equation of the slider-crank mechanism with a crack rod is established. The slider-crank mechanism with an open crack rod is investigated and then establishes the equivalent mechanics model by a massless torsional spring to simulate the influence of the crack in the rod, and the mechanism of a cracked rod is divided into two subsystems. The dynamical equation of the slider-crank mechanism is established by using Lagrange equation and Newton’s second law. They are cast in the USA from the original old patterns, and have a powder coated finish, not painted.
For example in certain application, the rotation of crank is considered as the input and the displacement of the slider is considered as the output. IntroductionThe precise relationship between the input and output is important for slider-crank mechanism. The calculated maximum Lyapunov exponent is positive, which shows that the movement of the slider in the crank slider mechanism with a cracked rod is chaotic.
Ugo Andresus, Paolo Casini use 2D quadrilateral to model the beam, then the natural frequencies (and the associated mode shapes) of the cracked cantilever beam were obtained , and they also use two-dimensional finite elements to consider the cantilever beam with an asymmetric edge crack as the plan problem and then conclude the behaviour of breathing crack which is simulated as a frictionless contact problem. Jin Zeng, HuiMa, Wensheng Zhang and RangchunWen mix elements by combining beam elements and solid elements to establish the finite element (FE) model for cracked cantilever beams and use the area damage factor to evaluate the crack levels. So, this behaviour should be studied. This kind of crack in the rod may cause the mechanism to exhibit nonlinear behaviour which should influence the mechanism dynamic when rod is activated according to crank rotating. Moreover, it is difficult to calculate the influence by normal formula directly, if there is a crack in the rod.
Guz use the boundary integral equation method to solve the fracture mechanics problem, and they impose the constraints to the normal and tangential components of the contact force and the displacement discontinuity vectors to take the contact interaction of the crack faces into account.In this work, a new idea is created to divide the slider-crank mechanism into two subsystems by crack point, and the crack is modeled by massless torsional spring. Ugo Andreaus, Paolo Baragatti, Paolo Casini, and Daniela Iacoviello present wavelet analysis for crack detection and quantification in beams based on static method, then the spatial wavelet transform is proven to be effective after comparing with the experimental study. Pier Francesco Cacciola and Giuseppe Muscolino model the cracked beam by finite elements in which the closing crack model is used to describe the damaged element. O.Giannini, P.Casini, and F.Vestroni use finite element that has a bilinear element matrix with the discontinuity passing through the origin to model the cracked zone of the beam. Andrea Carpinteri, AndreaSpagnoli, and SabrinaVantadori build up a general linear hardening rule for the fibers and a linear-elastic law for the matrix to assume an elastic-plastic crack bridging model.
Bell Crank Design Example Crack In The
The mechanism motion can be written as Lagrange equation and Newton’s second law. A cyclic bending moment M is considered to crank the mechanism, and the rods OA and AB are considered to be rigid. Equation of Motion on a Slider-Crank Mechanism without Crack in the RodA slider-crank mechanism without crack in the rod is modeled in Figure 1 to study the effect of dynamic motion. Motion Analysis of a Slider-Crank MechanismIn order to study the difference of slider-crank mechanism dynamic motion with and without crack in the rod, the equation will be created and simulation will be done based on the calculation. Comparing with the analysis results between the slider-crank mechanism with crack and without crack, the conclusion shows that it is necessary to study crack influence when analyzing the mechanical system dynamic performance and vibration characteristic. In this method, it is much easier to simulate the system with multiple cracks and easier to program by C language.
The total kinetic energy is , where T 1 is kinetic energy of rod OA, T 2 is kinetic energy of rod AB, and T 3 is kinetic energy of slider B. Represents the velocity of slider B. The center velocity of rod AB is , and its center angular velocity is. The mass of rod OA is m 1, and the mass of rod AB is m 2. The length of the rod OA is l 1, and then the length of the rod AB is l 2. The crank angle φ is the angle between rod OA and the horizontal direction.
Crack point C is at the middle of rod AB. Rod AB is considered to be composed of two rods AC and CB. Equation of Motion on a Slider-Crank Mechanism with a Crack in the RodA slider-crank mechanism with a crack in the rod is modeled in Figure 2 to study the effect of dynamic motion.
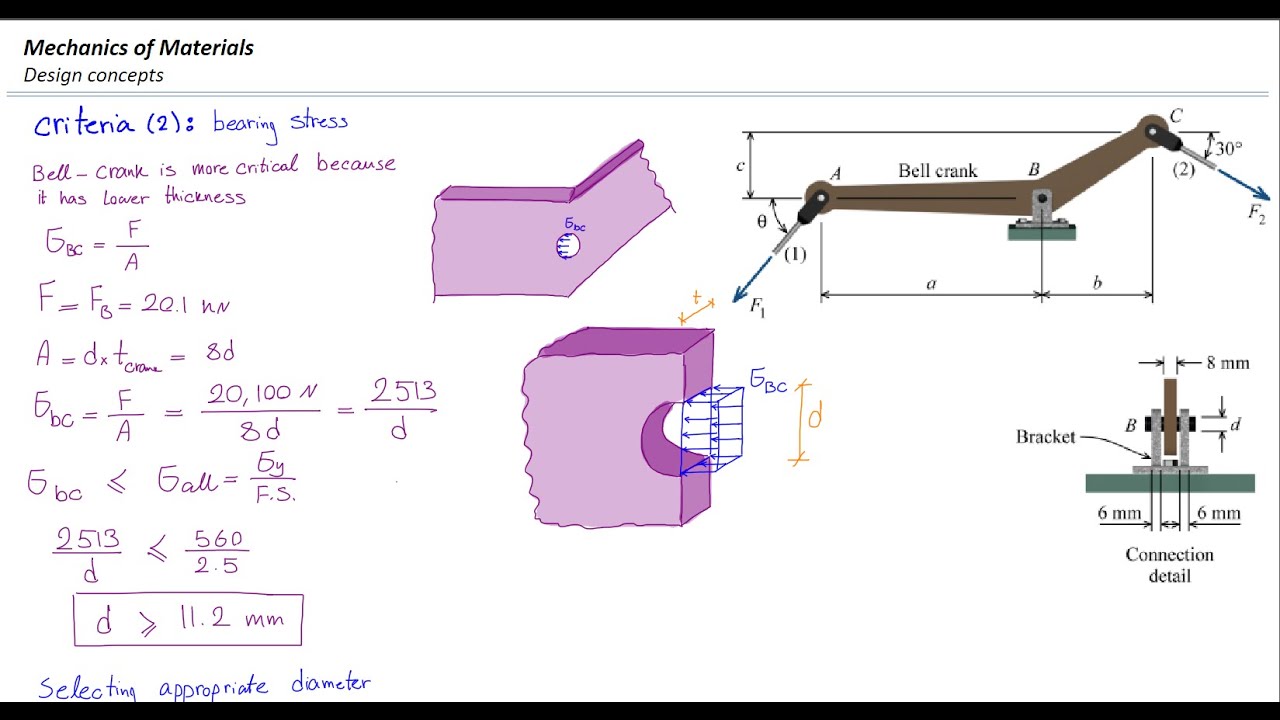
S is the distance for slider B. Is the angle between rod CB and the horizontal direction. Is the kinetic energy of rod CB. One can calculate the system 1 kinetic energy by the following formula: The generalized force can be written as One can write the Lagrange differential equation of motion as follows : The solution for the function is given as follows: For system 2, same as system 1, the generalized force can be written as One can write Lagrange differential equation as follows: The solution for the function is given as follows: The mass of rod CB is , and m 3 is the mass of slider B. The total kinetic energy for system 1 is , where T 1 is kinetic energy of rod OA, T 2 is kinetic energy of rod AC. Because rod AO and rod AB are considered as material uniform distribution, the mass of rod AC is m 2.
Then, the equation of slider-crank mechanism motion with a crack in the rod can be calculated as follows: 3. The bending moment of the torsional spring is where C is the flexibility of the rotation spring which can be influenced by crack depth d and cross section height h. Figure 3(a) is on crack dimension in the rod, and Figure 3(b) is on torsional spring.The equation of the deflection curve is where , p is the generalized force, and EI is the bending stiffness.The solution of ( 12) is where y(x) is the deflection, and the cross section bending angle is θ(x), bending moment is M(x), and one can calculate shearing force as follows : The flexible rod is considered as consistent on deflection, bending moment, and shearing force, so the relative angle of the torsional spring can be written as where is the relative angle between upper rod and the crack position, and is the relative angle between lower rod and the crack position. Cracked Rod CalculationThe rod AB is considered as flexible, then, to simulate the crack by massless torsional spring , which is shown in Figure 3. F is the external force on slider B.
The main reason is that SC1 is the linear system, but SC2 is the nonlinear system. There is no clear cyclic fluctuation for slider displacement on SC2. A summary of the properties of the experimental slider-crank model is given in Table 1.(1)There is cyclic fluctuation for slider displacement on SC1, and the displacement period 360deg can be easily found in the curve. Crack parameters used in calculation are as follows: crack depth d=6mm and cross section height h=30mm. The mechanism is cranked by a cyclic bending moment with regular angel velocity 300RPM (revolution per minute) which means the crank is driven one cycle every 0.2s.
